After sitting through the winter, the battery in the beetlebug was dead. After having the car for two years, this is only the third time the battery has gone flat. The first time was actually not from a lack of use at all. I was in the habit of starting the car up and letting it run every couple of weeks. I would let it heat up, then drive it back and forth in the driveway a few times to keep all the moving parts lubricated.
After one of those sessions, I found the battery was dead a couple of days later. It turns out the old style generators don’t charge at idle like more modern alternators. Letting the car sit and idle will actually run the battery down.
The battery is under the back seat. So, I flipped the passenger seat back forward and heard the terrible sound of seat cover ripping. One of the upholstery spikes on the bottom rail was fully extended. It tore a long gouge in the seat cover and new foam padding I installed last spring.
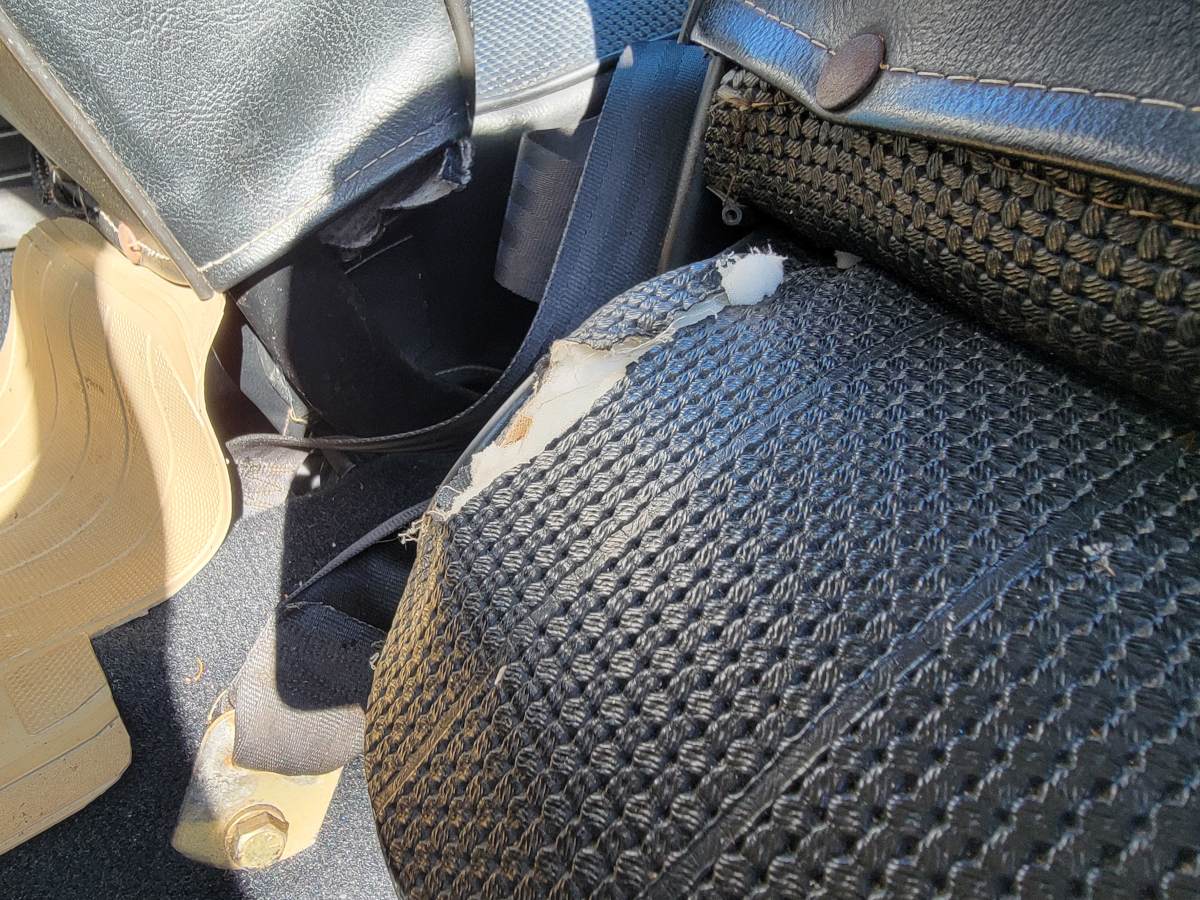
I connected jumper cables to my truck and started the car. I left the cables connected, hoping to get a better charge off the truck’s alternator. After letting it run for ten or fifteen minutes, I disconnected the jumper cables and turned off the car. When I turned the key, the battery was still completely dead.
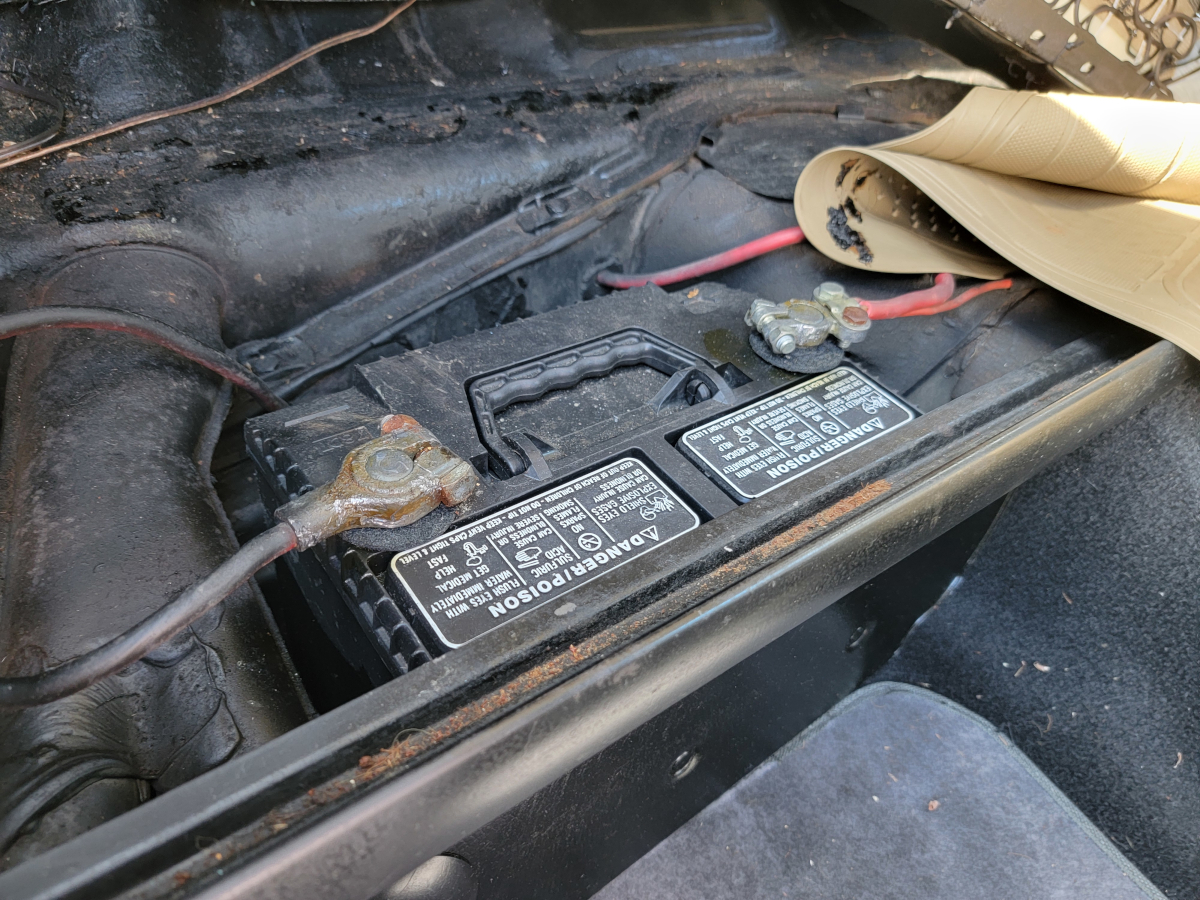
I was curious about the old battery. When I pulled it out, I noticed all of the labels/stickers/branding was gone. It has top and side posts and a handle, which is convenient.
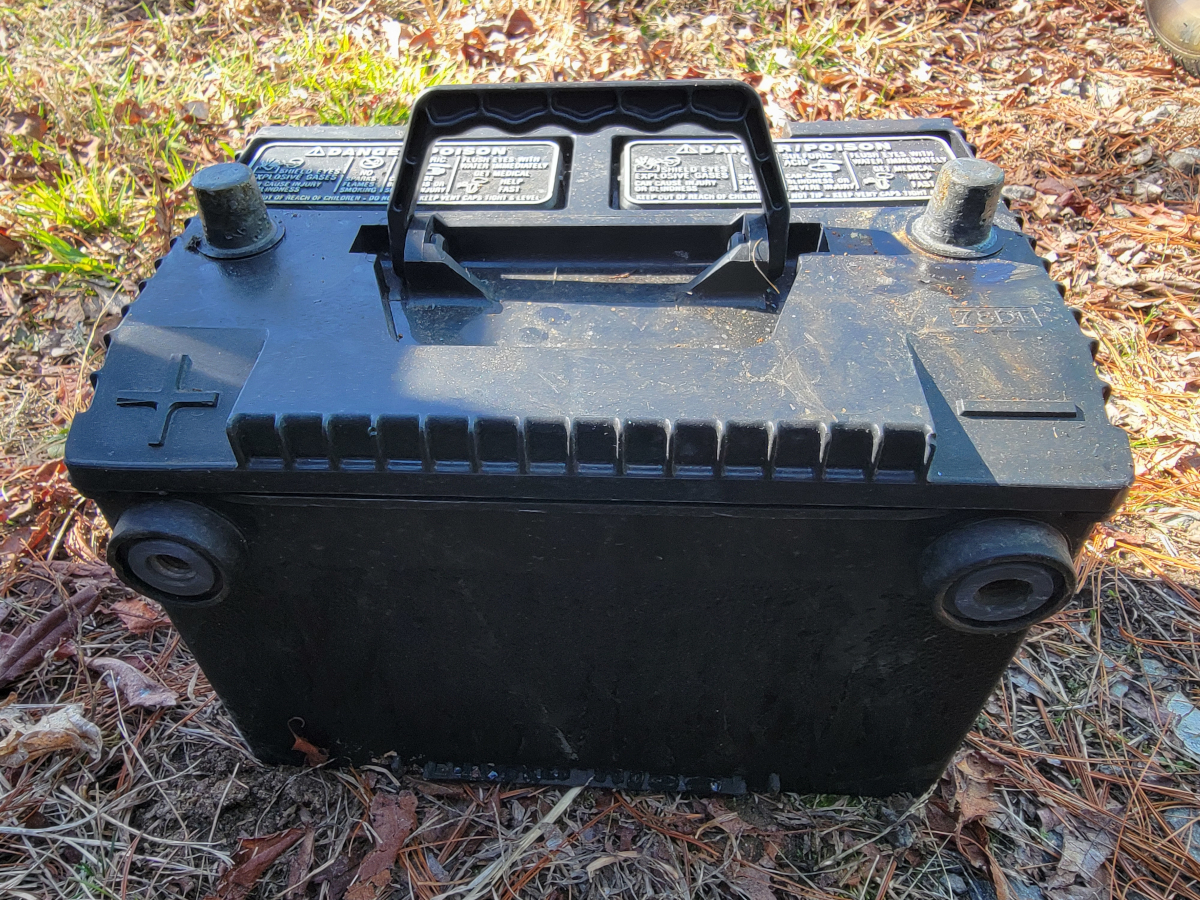
Something else caught my eye, it had condensation all over. I’m assuming that’s what happened to all the stickers.
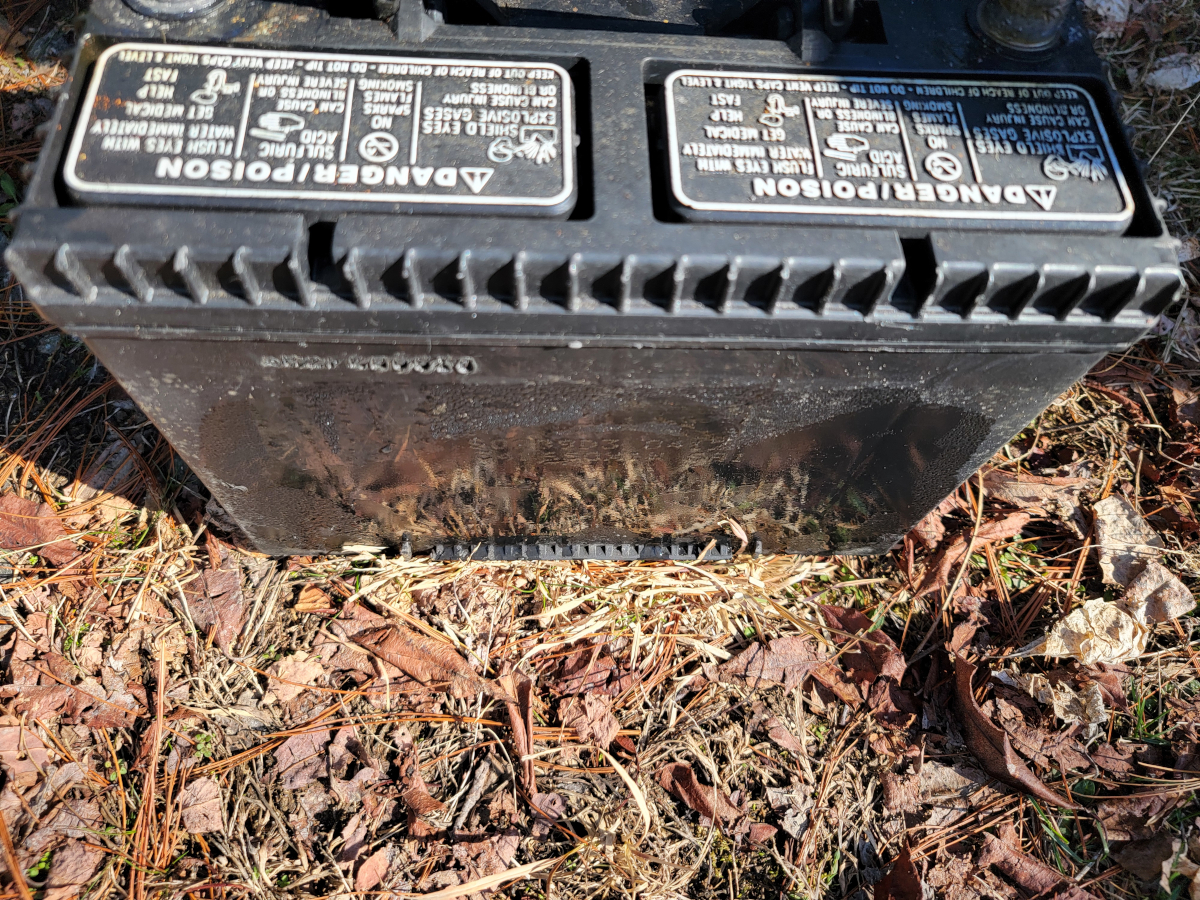
Next, I took the passenger seat out to repair the seat cover.
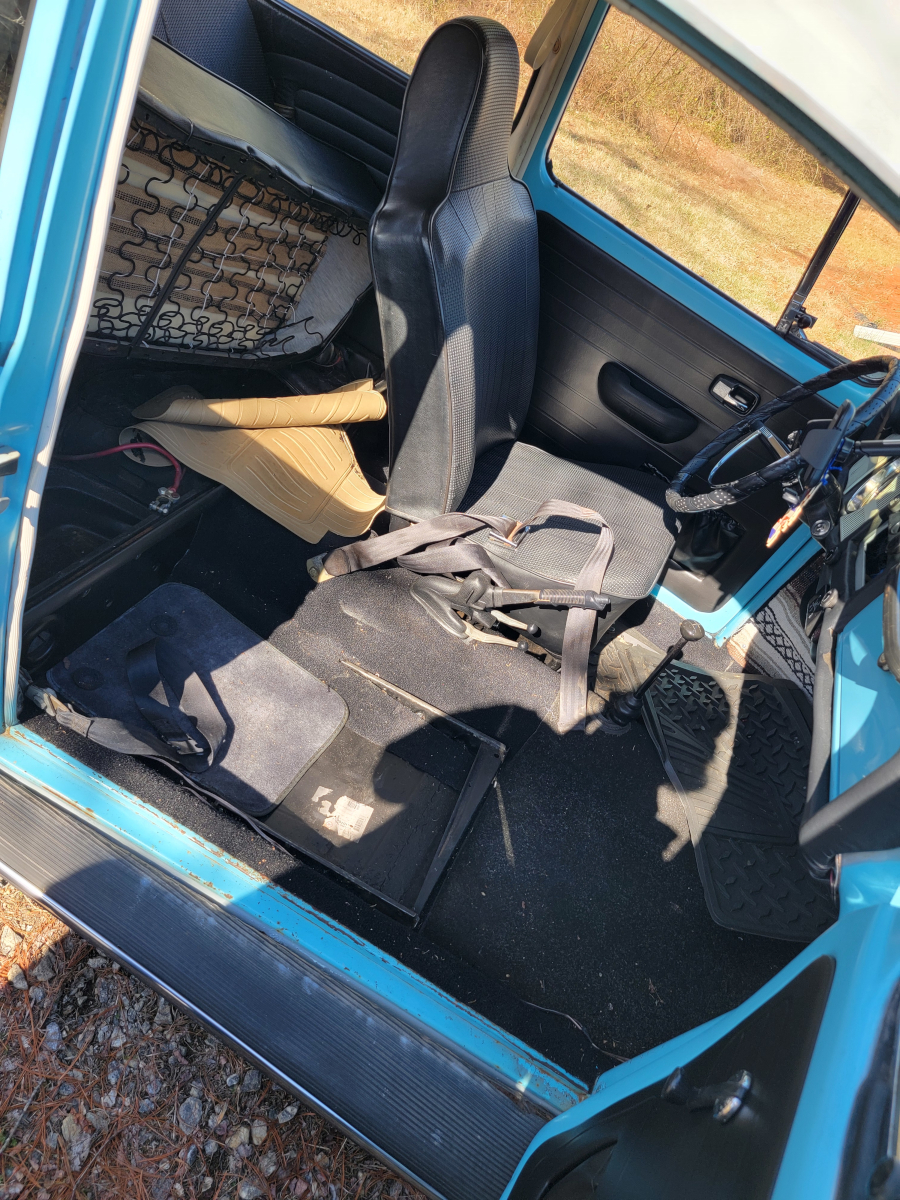
I carried the seat up to the porch to have a more stable place to work on it. I separated the two halves of the seat and found the offending article.
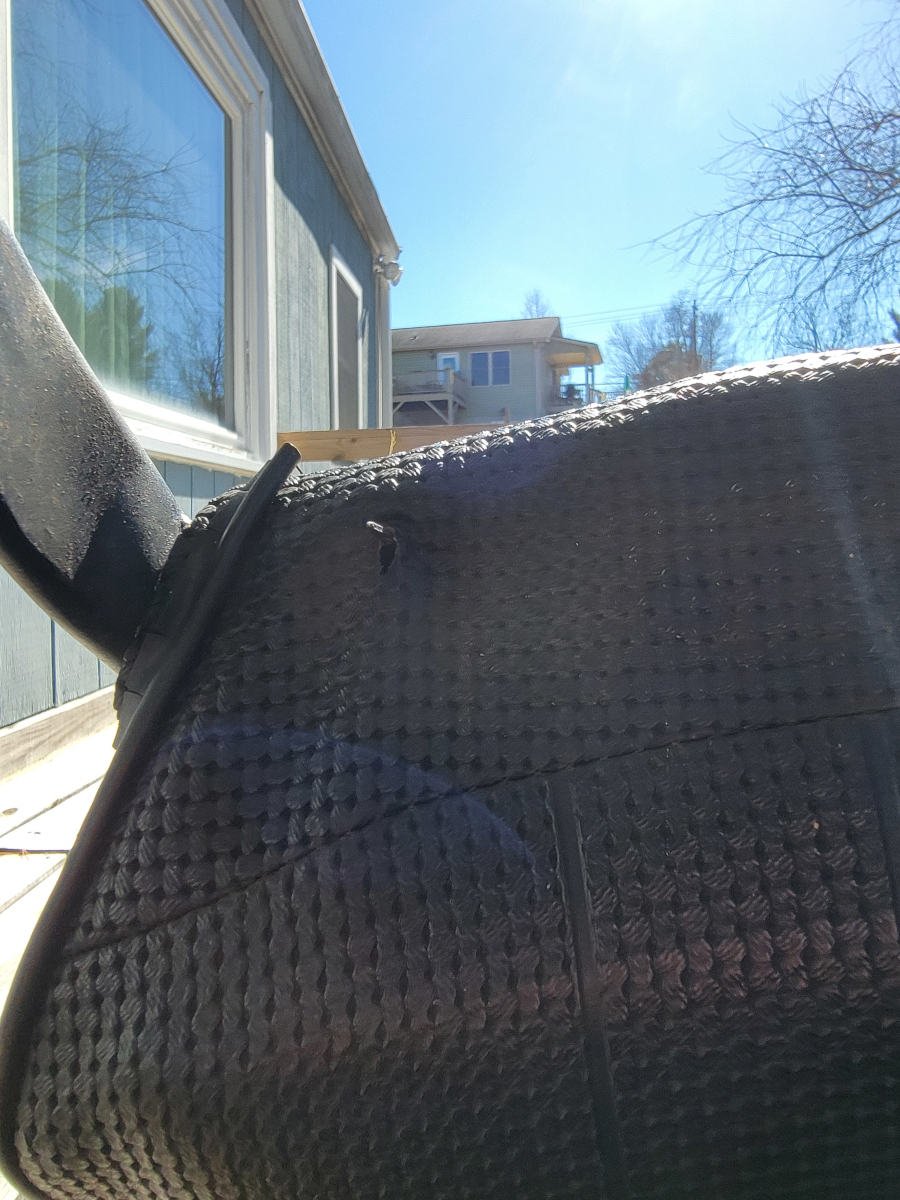
So, I pounded that one flat. The others in the area hadn’t found daylight through the seat cover, but they weren’t exactly out of harm’s way, so I flattened them as well.
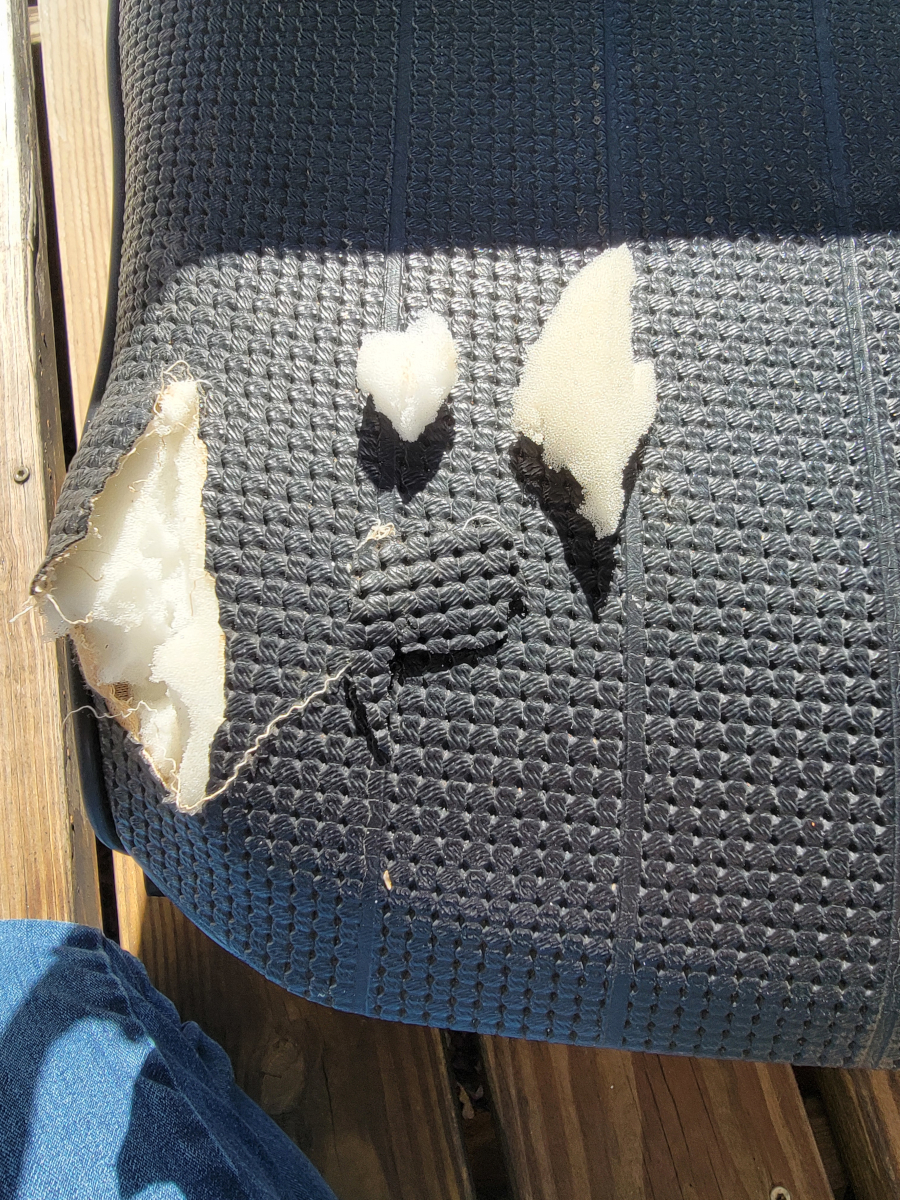
Taking inventory of the situation…
First, I glued the chunks of foam back into place with some Scotch Maximum Strength Adhesive I had laying around. In my experience, this stuff doesn’t hold up well over time. To be fair, none of the others that I have tried to either. Also, the nozzle broke in half, glued to the cap, so at least it sticks to its own packaging.
While I let that dry in the sun, I headed out to the parts store.
I haven’t purchased a battery in a few years and was surprised to find that prices have doubled. It was $194.99 for a Super Start Size 42 T5 – 42PRM (O’Reilly link).
I sprayed the anti-corrosion stuff on the terminals and installed the new battery.
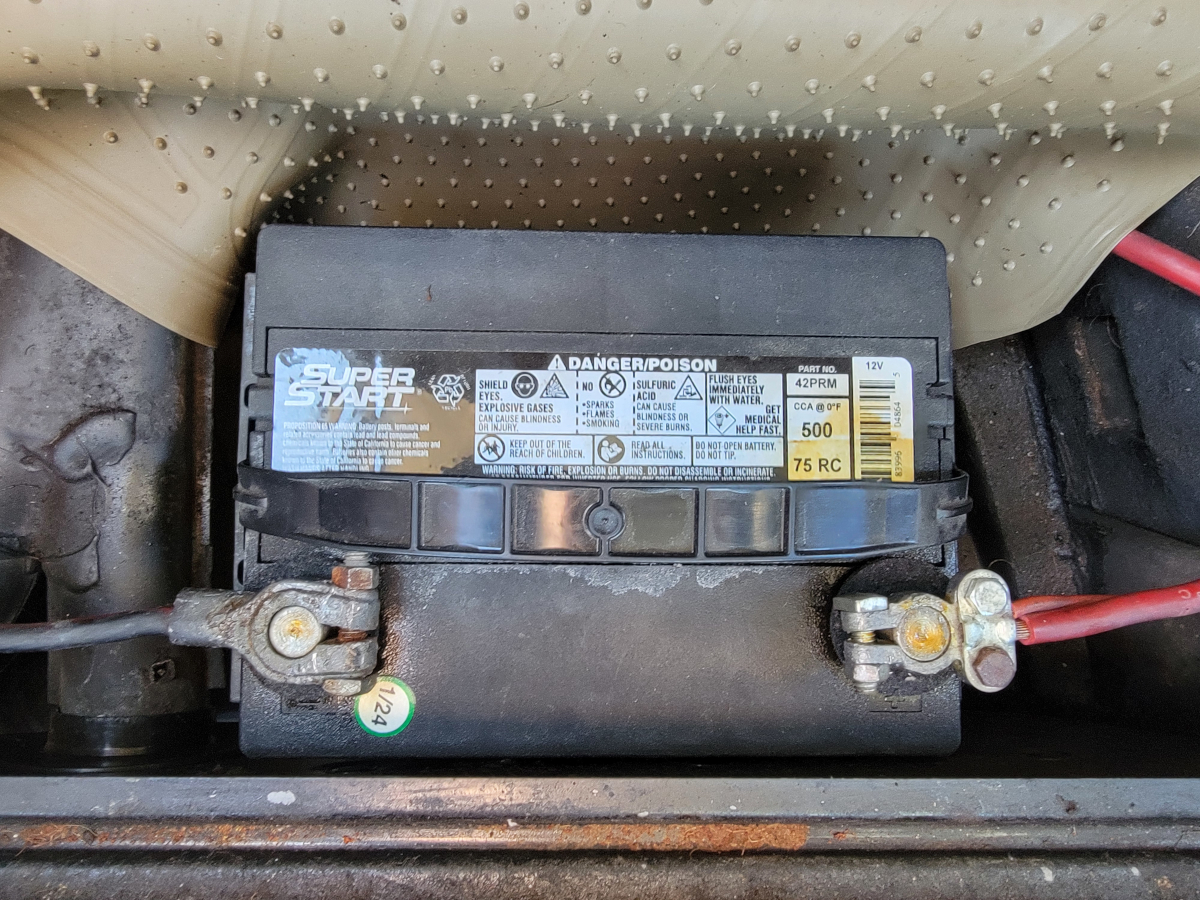
Back to the front (YOU WILL DO WHAT I SAY WHEN I SAY). Sorry.
Back to the front (YOU COWARD, YOU SERVANT, YOU BLIND MAN, BACK TO THE FRONT)
…seat, I cut an oversized piece of the black vinyl that I used to recover the dash pad last year. Because the patch piece was so much bigger than the hole in the seat cover, it took some creative contortion and origami to get it in there and laying flat.
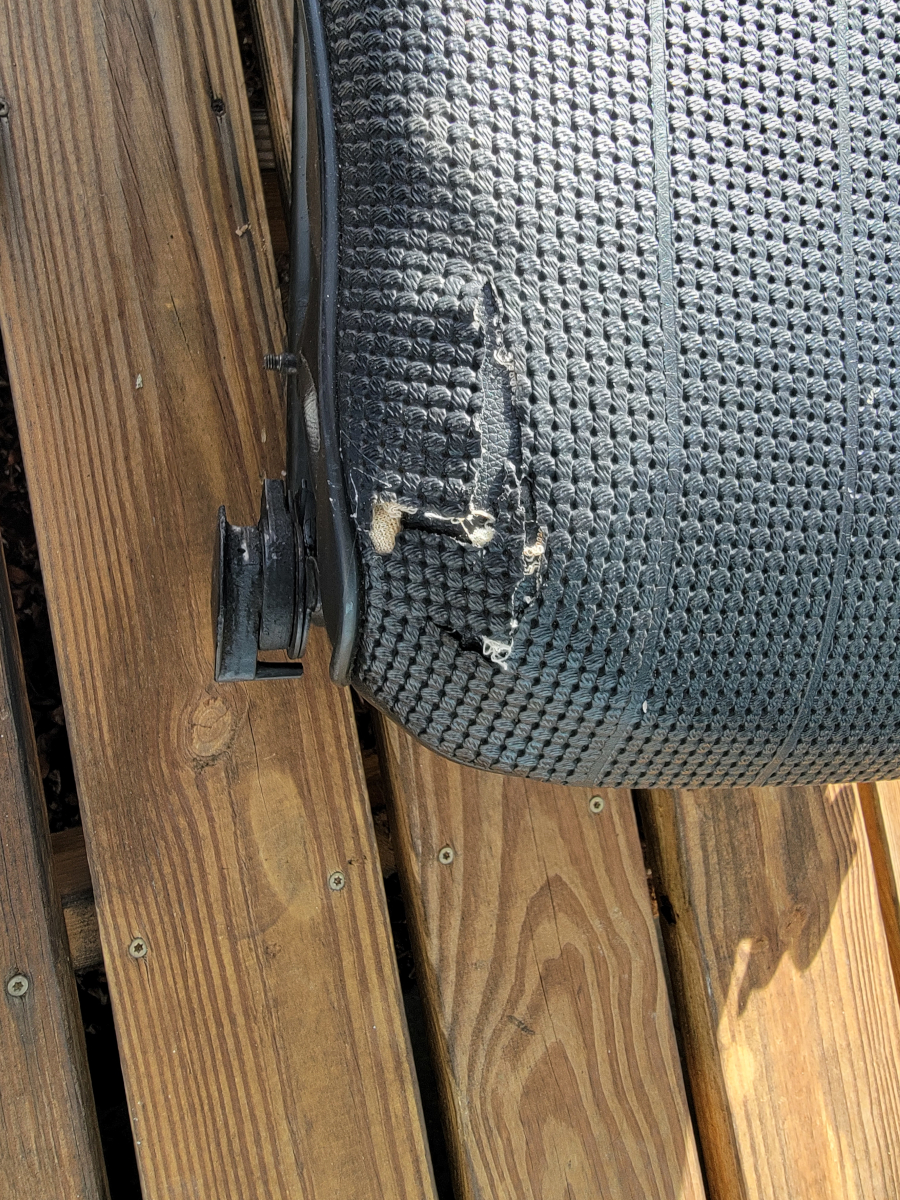
I used the rest of the tube of glue in between the vinyl patch and the shreds of seat cover to hold it in place. I thought about trying to stitch those edges together, pulling them tight. However, these old seat covers are so brittle, I knew the upholstery thread would have just pulled through.
It doesn’t look great as is, but luckily, the damage is at the back of the seat pad, right below the seat back. It’s not noticeable until you flip the seat back forward.